SafetySafety management system
Targets(FY2031) |
|
---|---|
Performance(FY2024) |
|
Measures |
|
Safety and Health Policy
The Daiseki Group establishes Safety and Health Policy at each company and promotes prevention of accidents, and Safety and Health.
We put safety as the top priority and work on creating the workplace where employees can work safely and healthy.
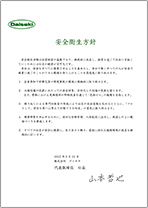
Safety and Health Policy(Daiseki)
Establishment of Safety and Health Management System
The Daiseki Group has an occupational health and safety management system with the president of each company as the chief responsible party and with parties responsible for health and safety appointed at every business site.
Also, we share information of accidents at the Daiseki Group to prevent similar accidents.
Daiseki’s Safety and Health Management System
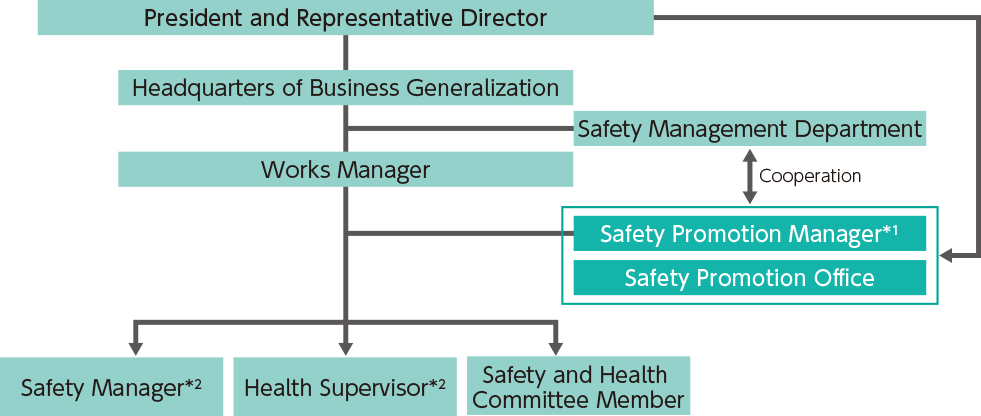
- * At the Chiba Works, which has less than 50 employees, it is not necessary to appoint a Safety and Health Manager, thus a Safety and Health Promoter has been appointed.
Daiseki has a system for sharing information and providing instruction concerning health and safety management inside the company, as follows.
- ●Safety promotion meetings held once a month, attended by parties responsible for safety promotion from the Headquarters of Business Generalization, Safety Management Department, and individual business sites
- ●Health and safety committee meetings held once a month at each business site
- ●Safety patrols conducted once a month at each business site
- ●Safety meetings in production divisions and business divisions of each business site
- ●In the event of an accident, the status of the accident and the response to it are reported to the president through the Headquarters of Business Generalization, and necessary instructions are issued by the president.
Safety Promotion Manager Appointment
“Safety Promotion Office” have been established at each Daiseki business site managed by “Safety Promotion Manager” appointed to promote safety. The president delegates the authority to promote safety to a person in charge at each worksite who provides guidance to staff and implements various safety measures. We have a system in which the General Manager of the Headquarters of Business Generalization (a representative director) supervises the Safety Promotion Offices of business sites through the Safety Management Department.
Safety and Health activities
At Daiseki, Safety Promotion Offices at each business site conduct the following occupational health and safety activities.
- ❶ Implementation of proper Danger Prediction Training
- ❷ Confirmation of acceptance work at customer sites
- ❸ Investigation of causes and sharing of information following accidents