SafetyAccident risk reduction
Efforts to eliminate unsafe condition
In order to eliminate unsafe work environments for drivers, we make improvements with customers ’supports as well. If improvements are difficult to make, we inform drivers of the risks and review work procedures, etc.
Also, Safety Management Department and Safety Promotion Office staffs ride together to the working sites and check the procedures, equipment and controls to make necessary improvements.
Unsafe conditions eliminated at Daiseki customers’ sites (2023)
Eliminated | In process or under negotiation |
---|---|
31 | 3 |
Learning from unsafe incidents
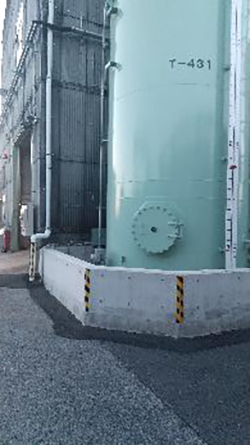
Preventing contact accidents by attaching tiger warning tapes on dikes (Chiba Works)
Daiseki implements a unsafe incident reporting system.
Among reported unsafe incident, those with a higher risk are discussed and addressed by a Health and Safety Committee. As an example of improvement, we have attached warning tapes to embankments to prevent vehicles driving inside the plant from coming into contact with the embankments.
No. of unsafe incident reports submitted in Daiseki
FY2024 |
---|
4,902 |